摘要:以六輥可逆冷軋機組為研究對象,介紹常見軋輥的缺陷,主要是軋輥的表面剝落缺陷。 從軋輥的使用、磨削、檢測等方面,提出了相應的預防措施和消除措施.關鍵詞:軋輥、剝落、措施THE ANALYSIS AND IMPROVEMENT FOR THE CAUSATION OF ROLLER SURFACE PEELING OFF OF THE SIX-ROLL REVERSING COLD ROLLING MILL
Abstract:This thesis takes the Six-roll Reversing cold rolling Mill group as its object of study, it introduces the common defect of the roller, mainly for the defect of peeling off from the suface of the roller. On the other hand, it proposes the provention and elimination methods accordingly from several aspects such as the roller usage, grinding inspection and etc.
key words:roller, peel off, method前言:軋輥是軋機的重要部件,軋輥的質量好壞直接影響軋機的運行,影響產(chǎn)品的產(chǎn)量質量和成本,冷軋過程中,軋輥表面承受著很大的擠壓應力和強烈的磨損,高速軋制時,卡鋼、過燒等會出現(xiàn)一些質量問題和質量缺陷,會造成輥面裂紋,因此,冷軋工作輥應具有極高而均勻的硬度,一定深度的硬化層,以及良好的耐磨性與抗裂性。以保證軋輥的使用要求和質量要求。所以分析軋輥缺陷產(chǎn)生的原因以及如何控制軋輥質量顯得非常重要,本文將從軋輥的合理使用,合理磨削,改善軋制條件加強檢測等方面研究控制軋輥質量,并對軋輥的常見缺陷提出相應的預防和糾正措施。1、使用情況廣東華美集團有一臺1450六輥可逆冷軋機組,2006年5月份安裝并試運行,在試生產(chǎn)過程中,由于軋輥使用不當及軋制工藝條件不成熟,造成了軋輥事故率多,消耗高,另一方面因換輥的頻繁,降低了軋機有效作業(yè)率,影響了小時產(chǎn)量和產(chǎn)品質量。2、軋輥常見缺陷軋輥的主要缺陷有輥面剝落(掉肉)及輥面磨損和輥身斷裂,其中輥面剝落是軋輥常見的缺陷和軋輥報廢的主要原因。3、軋輥輥面剝落的形成原因3.1一個是輥面產(chǎn)生裂紋向內(nèi)部擴展,最終造成剝落。軋制過程中金屬變形同時產(chǎn)生大量的熱。正常軋制時,熱量產(chǎn)生過程較為均勻并通過乳化液冷卻后帶出,對軋輥表面不會產(chǎn)生大的影響.軋制事故,包括粘鋼,打滑,跑偏疊軋,斷帶等等情況發(fā)生時,局部過多的熱量就會對軋輥表面產(chǎn)生熱沖擊。鍛鋼冷軋輥一般由Cr合金鋼經(jīng)過淬火及低溫回火制成.低溫回火的溫度通常不超過170ºC, 發(fā)生粘鋼等重大事故時,軋輥表面局部溫度可以達到800ºC甚至更高。軋輥表面受熱后,馬氏體基體會分解成碳化物和鐵素體,體積收縮,造成表面局部的拉應力,誘發(fā)表面裂紋;即使裂紋沒有立即產(chǎn)生,熱影響區(qū)的強度也會大大降低,這樣的輥如果進入軋制工況,也會產(chǎn)生軟區(qū)和疲勞裂紋, 這是軋輥表面裂紋的主要來源,也是最常見的軋輥缺陷產(chǎn)生原因。圖1圖2為出現(xiàn)粘鋼故障和打滑后工作輥表面出現(xiàn)的缺陷情況,可以看出,缺陷的顏色與其他地方差距很大,主要是粘鋼和打滑后產(chǎn)生的大量熱量將局部輥面相當于進行了回火,造成了輥面性能的不均,如果不及時消除這種缺陷繼續(xù)使用的話,很容易造成輥面的剝落,甚至報廢。圖3是一種更為嚴重的粘鋼事故造成的軋輥剝落,圖4 是一種軋輥表面裂紋缺陷,用肉眼根本無法看出和識別只有借助無損探傷儀才能發(fā)現(xiàn)。
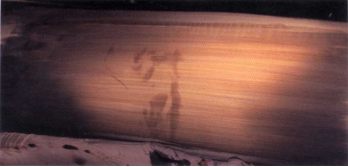
圖 1:在粘鋼軋機故障時產(chǎn)生的軟點(局部回火溫度過高)“暗”區(qū)比基體組織軟表面用20%的硝酸乙醇腐蝕液劑浸蝕。
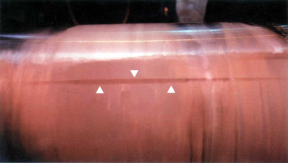
圖2:因打滑所產(chǎn)生的磨擦熱,在軋輥上形成的軟點“暗”區(qū)比基體組織軟表面用20%的硝酸乙醇腐蝕液劑浸蝕。

圖3:熱沖擊(更嚴重的熱裂紋形式)產(chǎn)生的剝落通常是因為軋機故障(粘鋼)等現(xiàn)象而產(chǎn)生的
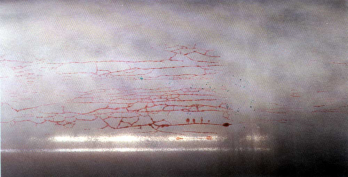
圖4:在磁粉探傷顯示下的冷軋機工作表面熱裂紋現(xiàn)象3.2二是由輥身淬硬層內(nèi)部的缺陷起源引起裂紋,并發(fā)展到表面引起的剝落,由于軋輥在冶金過程中近表面存在夾雜或其他缺陷作為裂紋源而引發(fā)的軋輥剝落。在軋輥表面的典型夾雜,是能夠看得見的,為縱向主軸的不規(guī)則形狀。其長度可為0.05mm~5mm(0.002”~0.020”)。清除夾雜材料后的留在軋輥表面上的“孔”表現(xiàn)粗糙,如圖5和圖6。

圖5軋輥表面的夾雜(50X)。
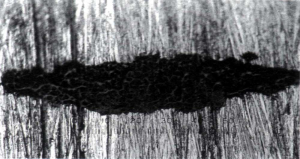
圖6圖5中所示夾雜的放大圖(200X)。4、預防輥面產(chǎn)生裂紋的措施4.1在使用方面首先優(yōu)化軋輥的更換周期,大量的資料表明,軋輥更換周期的長短直接影響軋輥的消耗,影響軋輥產(chǎn)生缺陷的幾率,軋輥更換過于頻繁,會過多的占用生產(chǎn)時間,造成有效作業(yè)率降低,生產(chǎn)產(chǎn)量降低,同時輥耗升高成本增大,反之軋輥更換周期過長,服役時間過長,會加劇軋輥疲勞,容易引發(fā)疲勞裂紋,同時對控制帶鋼板型控制帶鋼尺寸精度造成一定的影響,華美公司經(jīng)過大量的數(shù)據(jù)積累和經(jīng)驗摸索,將原來的更換周期調整如下:工作輥由原來的工作8小時調整為6小時,中間輥由原來的工作36小時調整為24小時,支撐輥為1個月,調整后的軋輥,工作狀況明顯改善。其次在使用過程中,冬天采取了一些措施:下機后的軋輥立即用棉被覆蓋,減少溫差的過大造成熱應力;上機前的軋輥(主要是指工作輥和中間輥)進行線外預熱;上機軋輥必須對輥面進行擦拭,減少異物硌傷軋輥;每班在換輥過程中抽輥必須檢查噴嘴的堵塞情況,保證輥面各處冷卻均勻。在乳化液控制上也進行了調整,主要是增大了濃度,保證充分的潤滑和軋制的順利;增大了乳化液的流量,使軋輥得到充分的冷卻,減少軋輥的熱應力;加大乳化液的維護,磁過濾系統(tǒng)充分發(fā)揮作用,有效清除乳化液內(nèi)部的鐵粉含量,減少軋輥的軟點生成,定期對板式過濾機進行過紙,凈化乳化液,定時定量添加軋制油和去離子水,確保乳化液指標的穩(wěn)定等等一系列措施,充分發(fā)揮乳化液的潤滑和冷卻作用,對減少軋輥事故起到了很好的作用。4.2磨削方面冷軋輥磨削的主要目的是:1)通過磨削軋輥消除軋輥輥面的疲勞層;2)消除加工硬化層或應力集中造成的表面微裂紋;3)使輥面硬度均勻;4)同時保證輥面有一定的粗糙度。所以磨削質量的好壞直接影響軋輥的質量和運行質量, 磨削量是一個重要的指標,磨削量過大,會增加磨輥工作量,重要的是輥耗升高;磨削量小,軋輥的疲勞層不能完全消除,表面微裂紋繼續(xù)存在,容易引起軋輥輥面剝落,不能起到磨削的目的。根據(jù)生產(chǎn)實際情況和大量數(shù)據(jù)的積累摸索,最終確定軋輥的磨削量為:正常下機的軋輥,工作輥0.15-0.2mm,中間輥為0.5-0.6mm,支撐輥為1.0mm以上,非正常下機的軋輥是將缺陷磨盡再按照正常下機的軋輥進行磨削;同時也調整了磨削的輥面粗糙度,由原來的0.3um改為現(xiàn)在的0.7um,以改變軋制摩擦系數(shù),減少帶鋼打滑現(xiàn)象。4.3檢測方面我們配備了超聲波探傷儀,用于檢測軋輥表面、近表面和深層的裂紋,包括了使用過程中造成的表面微裂紋,軋輥制造中內(nèi)部的夾雜缺陷以及裂紋缺陷,因為軋輥是否有缺陷,光由肉眼觀測是不夠的,有時是根本不能發(fā)現(xiàn)的,尤其是遭遇軋制事故,表面受到過熱沖擊的軋輥,經(jīng)常會沒有明顯開裂,但軋輥表面已經(jīng)有損傷,如熱影響區(qū)和微裂紋,這些缺陷只有通過表面探傷的方法才能夠將其檢查出來.通過檢測,有效的減少了因裂紋繼續(xù)擴展造成的輥面剝落,避免了因軋輥制造缺陷如內(nèi)部裂紋和夾雜等造成的軋輥事故,對于事故輥經(jīng)過表面探傷后,對缺陷部分要求在磨削時全部磨盡,再按正常下機輥進行磨削,直到再次檢測沒有裂紋為止,應該說軋輥探傷不僅對軋輥的缺陷和表面疲勞層是一個消除作用,同時對摸索合理的軋輥磨削量也有一定的好處,通過檢測有效避免了缺陷輥的繼續(xù)上機使用,杜絕了因此造成的軋輥輥面剝落。4.4軋制工藝的優(yōu)化在生產(chǎn)過程中我們根據(jù)不同廠家的熱卷原料情況和帶鋼的性能狀況,制訂合理的軋制工藝,盡力使各道次的壓下趨于均勻,軋制力基本相當,減少因負荷的過大造成軋制事故損傷軋輥;同時對一些好的生產(chǎn)小竅門進行推廣,比如帶頭入鉗口方法,軋制過度段的調整法等等,都對減少軋制帶鋼跑偏和軋制事故有很大的效果,減少了生產(chǎn)事故和軋輥事故的發(fā)生。5、結論通過以上原因分析和有效措施的采取,軋輥事故明顯減少,表面剝落缺陷近一年內(nèi)沒有再發(fā)生,輥耗也得到了有效降低,取得了很好的經(jīng)濟效益。參考文獻[1]楊利波,周濤等 HC可逆冷軋機軋輥失效改進措施的試驗研究 鋼鐵,2006.5[2]王春杰 淺析冷軋輥表面剝落原因及改善 江蘇冶金 2001.3